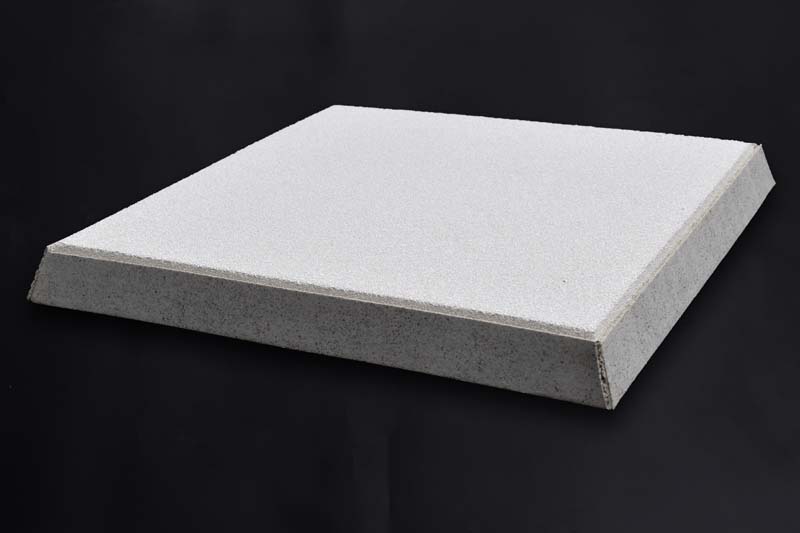
23 8月 Nikkeikin Act Ceramic Foam Filter
Nikkeikin Act Ceramic Foam Filter is the most effective way to remove inclusions in aluminum melt.
The ceramic foam filter has a multi-layer network, multi-dimensional through-holes, and the pores are connected to each other.
During filtration, the molten aluminum carries inclusions along the tortuous channels and pores, and is directly intercepted, adsorbed, and deposited when it comes into contact with the foam skeleton of the filter plate.
When the melt flows in the hole, the filter plate channel bends, the melt flowing through the channel changes the flow direction, and the inclusions collide with the hole wall anvil and firmly adhere to the hole wall.
Ordinary aluminum castings usually use 10-40ppi ceramic filter plates.
Aviation and high-quality aluminum materials usually use 30-60ppi ceramic filter plates.
Therefore, the 30ppi 40ppi cast filter is the most commonly used ceramic foam filter in the aluminum casting industry. Please contact sales@adtechamm.com to purchase.
Nikkeikin Act Ceramic Foam Filter effectively eliminates solid inclusions in molten metal, so aluminum alloy can successfully obtain high-quality aluminum products through forging, aluminum foil manufacturing, and extrusion processing. The product has a selection range of 10ppi coarse holes to 70ppi very fine holes, so there will always be a product standard that suits your requirements. Both ordinary and special sizes required by customers can meet the requirements.
The 30ppi cast filter has natural chemical adsorption capacity (affinity) and can adsorb impurities such as molten alumina.
The impurities in the molten metal (including particles smaller than the pore size) are adsorbed on the inner wall of the hole to improve the filtering effect.
The advanced extrusion production process makes the ceramic filter have a unique square and triangular design, thereby increasing the contact area with the ceramic.
Improve the filter’s ability to absorb and trap small impurities, which is better than non-extrusion filters, and the molten metal flows smoothly.
Improve pouring speed and continuity.
Reduce casting scrap rate.
Improve the mechanical properties of castings and prolong the service life.
No Comments