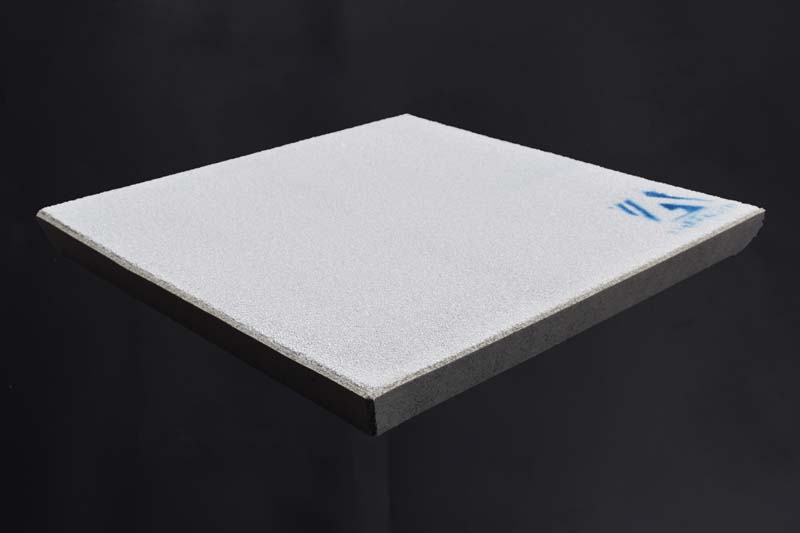
23 8月 Nikkeikin Ceramic Foam Filter
Nikkeikin Ceramic Foam Filter is installed on the CFF BOX machine to filter the liquid impurities in the aluminum alloy to meet the high value-added, high-tech performance aluminum alloy precision casting production for aviation and transportation.
In the process of aluminum smelting and casting, the purity of the aluminum melt is related to the metallurgical quality of the ingot.
The most common filtering method is to use a filter plate to filter out impurities in the molten aluminum. Usually, cast filter production is placed directly in the filter box for filtration.
Liquid aluminum filter box is an auxiliary tool that can improve this situation. We put the filter plate in the liquid aluminum filter box. The molten aluminum is repeatedly filtered through several layers of filter plates, which greatly improves the metallurgical properties of the ingot.
Oxidation slag
Analysis on the Causes of Aluminum Alloy Oxidation and Slag Inclusion Defects
1. The charge is not clean, and the return charge is too much.
2. The slag in the alloy liquid is not removed.
3. After the deterioration treatment, the rest time is not enough.
Preventive measures
After the charge is blown by sand, the return charge is controlled within 70% of the mass of the charge.
Degas and remove slag thoroughly; after deterioration, ensure that there is enough standing time to allow the slag to sink or float.
Use Casthouse Filter to remove oxide slag and other aluminum slag.
Nikkeikin acquired Filter Foundry through sales@adtechamm.com for continuous casting, semi-continuous casting, gravity casting and low pressure casting aluminum flux filtration equipment.
The technical staff of Alitalia believes that the ceramic foam filter is an effective tool to achieve the metallurgical purity of the molten metal during the casting process. The filter can also stabilize the filling of the mold, thereby preventing undesirable defects in the casting.
Nikkeikin Ceramic Foam Filter usually uses polyurethane foam as a carrier, immersed in a ceramic slurry made of fine powder (such as refractory aggregate sintering aids, binders and water), and then extrudes the excess slurry. The ceramic material around the foam fiber is dried, fired and sintered at a high temperature, and finally the foam ceramic product is left.
Because the casting temperature of the casting alloy is different, the foam ceramic filter made of refractory material should be used when casting.
In order to solve this problem, a simple filter made of wire mesh, perforated steel plate, etc. is inserted into the gating system to remove impurities from the beginning.
Inner filter with two-dimensional structure such as silicate needle fibers and boron nitride fibers.
Nowadays, ceramic foam filters use pore sizes to mechanically intercept large mixed oxide particles, while filter cakes are used to filter small mixed oxide particles.
It also has the functions of adsorption and rectification. The production line using ceramic foam filters has significantly increased the output of castings.
No Comments