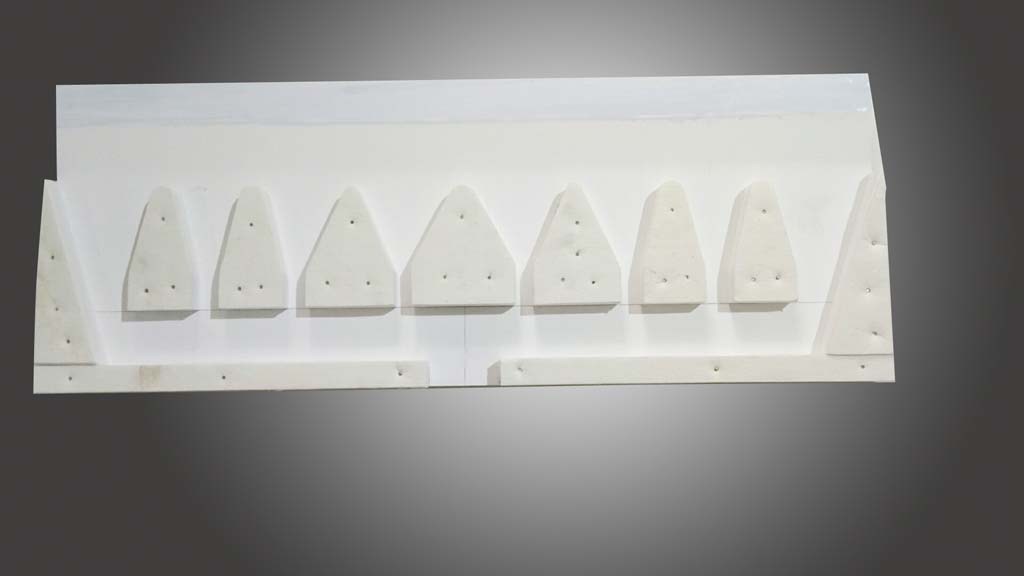
30 11月 Nozzle Cavity
Nozzle Cavity is a key part of conveying molten aluminum in aluminum alloy casting and rolling production. The nozzle structure will directly affect whether the melt can enter the casting-rolling zone from the nozzle cavity uniformly and stably, thereby affecting the quality of the plate.
The shunt blocks inside the casting nozzle are arranged in an orderly manner, thereby improving the uniformity of the melt distribution in the casting nozzle and improving the quality of the cast-rolled products. It plays a key role in stabilizing the casting and rolling process and quality. If you need, please contact sales@adtechamm.com for more details and price.
Scientifically composed of ceramic fibers and inorganic ceramic materials, it has the advantages of moderate elasticity, small deformation, and long service life.
It can effectively prevent the corrosion of molten aluminum to the cavity of the casting nozzle, thereby providing an effective guarantee for the quality of cast-rolled aluminum plates. According to customer requirements, casting nozzles of various models and supply methods can be made.
According to the boundary layer theory of fluid mechanics, after the aluminum melt enters the nozzle cavity, it flows in the direction of the nozzle outlet with the least resistance under the action of the static pressure of the liquid surface of the front box.
The flow velocity in the central area away from the boundary of the nozzle is greater than the boundary area, and a shunt block must be set inside the nozzle to ensure that a part of the melt flows to both sides after encountering resistance in the middle.
During the casting and rolling process, the melt flow in the cavity is required to be stable, and the melt heat flow field at the exit of the nozzle is uniformly distributed in the width direction, so the shunt blocks must be reasonably distributed.
High-speed thin strip twin-roll casting is a short-flow, near-net-shape processing technology. Its casting-rolling process belongs to the category of sub-rapid solidification, and its cooling rate is between 102°C/s and 104°C/s.
The technology specifically has the advantages of refining crystal grains and suppressing segregation, can improve the microstructure of the product, bring excellent subsequent processing performance, and can produce products that are difficult to produce under ordinary process conditions.
Due to its technological characteristics, this technology requires a fast cooling rate of the molten metal during the casting and rolling process, and a reasonable flow field distribution in the nozzle cavity, otherwise the quality of the thin strip product and the stability of the casting and rolling production process are difficult to guarantee.
Nozzle Cavity structure and assembly are the key components that affect the flow field and temperature field distribution in the nozzle cavity. Therefore, it is necessary to develop a new type of casting nozzle with stronger cooling capacity and more reasonable flow field distribution in the nozzle cavity.
Sorry, the comment form is closed at this time.