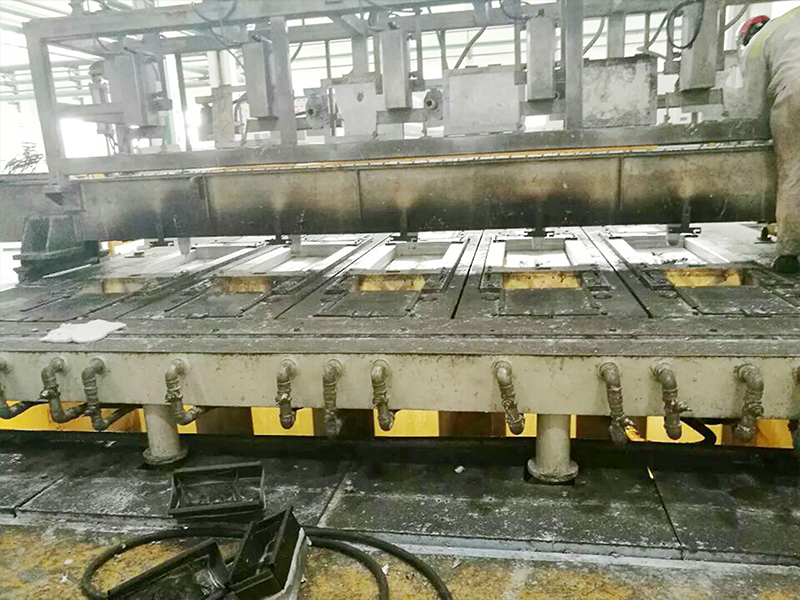
05 3月 Refractories for Continuous Casting
Refractories for Continuous Casting refers to materials made by melting, crystallization, annealing and cold working of raw material batches.
Since the energy used for batch melting is mainly electric energy (resistance heat, arc heat and high-frequency energy of electromagnetic field), this type of material is usually called fused refractory.
Continuous casting is an advanced casting method. Its principle is to continuously pour molten metal into a special metal mold called a crystallizer. The solidified (crusted) casting is continuously poured from the other end of the crystallizer. Pull out, it can get any length or specific length castings.
The development of continuous casting is an important means to optimize the structure of China’s metallurgical industry, which will fundamentally change the low efficiency and high consumption status of China’s metal material production, and promote the development of product structure in the direction of specialization.
The development of advanced continuous casting technologies such as near net shape continuous casting, single crystal continuous casting, high-efficiency continuous casting, continuous casting billet hot delivery and hot charging will be very active, and will drive the research and development of a series of new materials.
Application of Refractories for Continuous Casting in the aluminum industry
In the world’s non-ferrous metal production, the annual output of aluminum has always been the first, far exceeding other non-ferrous metals. The amount of refractory materials consumed by the aluminum industry each year is much more than the total amount of refractory materials consumed in the smelting of copper, lead and zinc.
According to the process of aluminum smelting industry, Refractories for Continuous Casting is divided into two categories, namely refractories for electrolytic aluminum and refractories for aluminum smelting furnaces.
The production of modern electrolytic aluminum industry uses cryolite-alumina molten salt electrolysis.
Molten cryolite is the solvent, alumina is used as the solute, the carbon body is used as the anode, and the aluminum liquid is used as the cathode. After a strong direct current is applied, the electrochemical reaction is carried out on the two poles in the electrolytic cell at 900°C-1000°C. The electrolyte and the aluminum are kept in a molten state, the aluminum liquid is discharged from the tank at intervals, and a quantitative amount of alumina and cryolite are added to the tank.
Because the electrolytes such as cryolite added in the electrolysis process cannot be fully electrolyzed, the excess part and the gas phase above the melt will cause serious corrosion to the refractory.
The aluminum smelting furnace is a new type of high-efficiency and energy-saving aluminum melting furnace developed based on the aluminum smelting process. It can well meet the requirements of strict alloy composition, discontinuous production, and large single furnace capacity in the aluminum smelting process. Reduce consumption, reduce burning loss, improve product quality, reduce labor intensity, improve working conditions and increase production efficiency.
During its working process, since the viscosity of molten aluminum at 750°C is quite close to that of water at 20°C, it is very easy to penetrate into the furnace lining and cause chemical reactions; when the molten aluminum is in contact with refractory materials, Oxides such as Si02, Ti02, Fe0 in refractory materials are easily reduced by aluminum, causing nodules, bulges and precipitated debris on the surface of the furnace lining.
During the operation of the furnace, the molten metal in the furnace constantly churns and stirs, constantly scouring and abrading the furnace lining, and the part impregnated by the molten aluminum is in danger of infiltration and cracking, and it will also cause spalling when the furnace is shut down.
Therefore, the furnace lining material in contact with the molten aluminum must have high thermal stability and as little impregnation as possible, while also requiring high mechanical strength and hardness.
No Comments