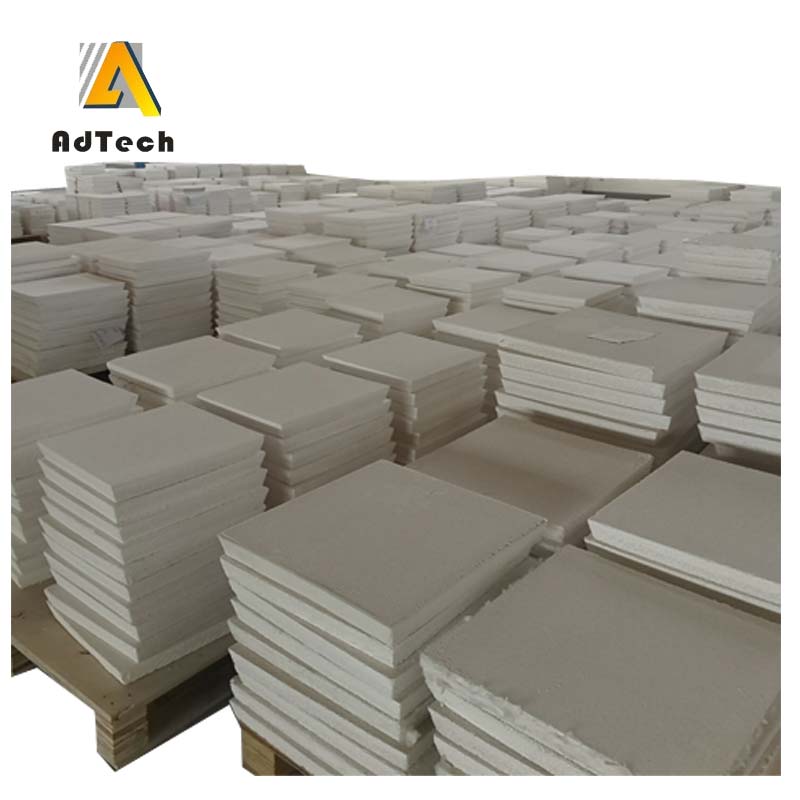
15 7月 Refractory Material Ceramic Foam Filter
Refractory Material Ceramic Foam Filter
Refractory Material Ceramic Foam Filter for temperatures up to 1250 ° C for filtration of aluminum and alloy solutions.
Refractory Material Ceramic Foam Filter To meet the ever-increasing quality of aluminum castings, the use of Ceramic Foam Filter CFF is becoming more and more important. Filters are also widely used in ordinary sand casting such as tidal casting and casting of permanent molds such as automotive aluminum parts casting.
Refractory Material Ceramic Foam Filter uses a filtration process based on the following considerations. On the one hand, the filtration makes the flow of aluminum liquid orderly and relatively calm, while on the other hand, the solid slag in the molten metal is effectively removed, and the quality of the casting is rapidly improved.
Refractory Material Ceramic Foam Filter effectively removes solid inclusions from molten metal, so aluminum alloy can be smoothly forged, aluminum foil, and extrusion processes to obtain a perfect aluminum product.
The product has a range of 20 ppi coarse pores to a very fine pore size of 60 ppi, so there will always be a product standard that suits your requirements. Both the normal size and the special size required by the customer can meet the requirements.
Refractory Material Ceramic Foam Filter Porosity
Porosity is the percentage of the total volume of the cavities in the filter plate product to the total volume of the filter plate product.
Porosity determines the filtration capacity of the foam ceramic filter plate per unit volume.
The larger the porosity, the larger the filtration flow rate of the filter plate and the stronger the filtration capacity.
Inspect and clean the surface of filter bowl, keep it clean and intact.
Gently lay the filter in the filter bowl, press sealing gasket around the filter by hand to prevent molten aluminum from dispersing or floating away.
Use electric or gas burning to preheat filter bowl and ceramic foam filter evenly for 15-30 minutes, make sure their temperature close to molten aluminum. The preheating temperature for ceramic foam filter should above 260℃. Expanding cotton will seal after preheating. This procedure makes ceramic foam filter steady fixed in molten aluminum. Preheating also leads ceramic foam filter pores open and avoid occlusion caused by thermal expansion and contraction.
Observe the change of molten aluminum height, hold molten aluminum flow in standard needs. Normal starting molten aluminum height is 100-150mm. The height falls down below 75-100mm when molten aluminum flows, and it will slowly increase later.
Do not hit or shake ceramic foam filter in filtration. At the same time, control molten aluminum flow rate in launder, never to be too much or too little.
Take out ceramic foam filter and clean filter bowl in time after filtering.
There are currently two main methods for determining porosity.
One is to calculate the volume of the hole in the filter plate according to Archimedes’ law, that is, to inject water into the glass beaker with the overflow pipe until the water flows out from the overflow pipe.
The water will be tested when the water is no longer flowing out.
All the samples are gently placed in the water, then the water flows out of the overflow tube, and the volume of water in this part is measured.
The volume of the overflow water is subtracted from the physical volume of the filter plate, which is the total volume of the holes in the filter plate.
Another method is to separately determine the true density and bulk density of the sample to be tested, and then calculate the porosity of the sample according to the following formula.
These two methods have their own advantages and disadvantages.
The method of operation is simple and convenient, and the detection speed is fast, but its fatal weakness is due to the water absorption characteristics of the filter plate material itself, so that the volume of water discharged is smaller than the actual one. This causes the measured data to be too small.
Although the test process of the second method is more complicated, the influence of the water absorption of the filter plate material is excluded during the test, and the obtained data is relatively accurate.
The index of porosity is determined to be greater than 84% in this standard.
Sorry, the comment form is closed at this time.