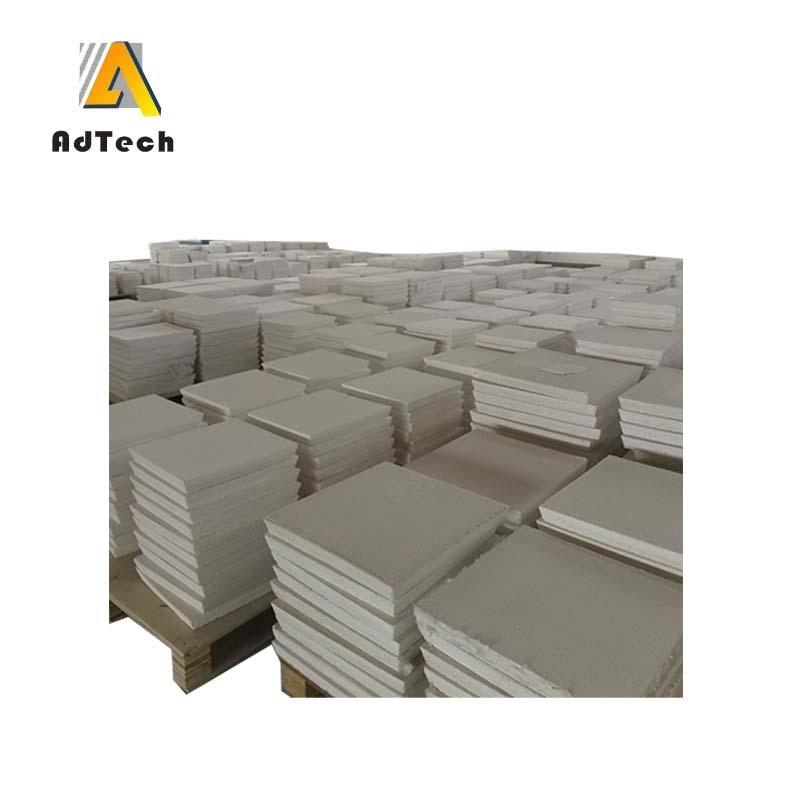
15 7月 Silican Carbide Ceramic Filter
Silican Carbide Ceramic Filter
In casting production, steel castings, cast iron parts, cast aluminum parts and other alloy castings are prone to quality problems such as slag, blisters and gas eyes due to various reasons.
Therefore, the removal of non-metallic inclusions in the metal melt has great technical and economic value for improving the yield of castings and improving the quality of castings.
Silican Carbide Ceramic Filter removes bubbles, ash oxides, and various assimilated impurities in the aluminum melt, greatly advances the product rate of aluminum castings, the quality of the traveling aluminum products, and prevents other metal components from infiltrating into the aluminum solution. The shortcomings do not affect the aluminum alloy factor to ensure the quality of aluminum castings.
Improve the performance of aluminum casting machines: the hardness of the casting can be advanced, and the contour hardness is averaged and the bending strength of the casting is improved.
Silican Carbide Ceramic Filter is widely used in various casting processes and production of various metal castings. It can effectively remove harmful inclusions in metal solutions, eliminate defects such as gas, scum, and blisters in castings, and reduce the rate of defective products. More than 90%, improve the intrinsic quality and appearance quality of castings, reduce energy and labor consumption, and significantly increase the economic and social benefits of casting manufacturers.
Foam ceramic filter plates are available in a wide range of sizes and are suitable for use in all aluminum processing industries, such as electrolytic aluminum plants, strip processing plants, foil processing plants, tubular bar processing plants, and recycled aluminum ingot plants.
The quality of the aluminum melt is important, which greatly affects the subsequent processing properties and the quality of the final product. Therefore, all countries in the world are very fond of the purification of aluminum melt.
During the smelting process, aluminum is exposed to the furnace atmosphere in a molten or semi-molten state, which is prone to oxidation, easily reacts with water vapor to absorb hydrogen, and easily forms various forms of non-metallic slag (such as furnace lining debris, chlorine in the flux). Compounds, carbides, etc.) as well as coarse intermetallic particles and the like.
Aluminium Ceramic Foam Filter production process
The Ceramic Foam Filter uses a three-dimensional network structure and an organic foam sponge connected to the pores as a carrier, invading it into a special ceramic slurry with thixotropic properties, and adopting a special roll extrusion process to uniformly apply the ceramic slurry to the skeleton of the carrier. Then, it is dried and solidified and then fired at a high temperature.
Porous Ceramic Foam Filter Foam Ceramic Filters for Aluminum Alloys Since the first research in 1978, foam ceramic filtration technology has developed rapidly.
Porous Ceramic Foam Filter uses polyurethane foam as a carrier, immersing it in a coating made of ceramic powder, binder, sintering aid, suspending agent, etc., and then extruding excess coating to uniformly apply the ceramic coating to the carrier. The skeleton becomes a green body, and the green body is dried and fired at a high temperature.
Aluminium Ceramic Foam Filter transmittance
Transmittance refers to the effective filtration area of the foam ceramic filter plate product. The higher the light transmittance, the less blind holes are, and the more effective the filter holes (potholes), the better the filtering effect.
The foam ceramic filter plate to be inspected is placed on a light box with a built-in 200W incandescent bulb, and the square transparent plastic plate with a uniform 5.0×5.0 mm square is used to measure the area of the large surface of the filter plate, so as to calculate the test. The light transmittance of the filter plate is used to determine the light transmittance of the filter plate. In this standard, the transmittance (through-hole ratio) of the filter plate is specified to be 95% or more.
Sorry, the comment form is closed at this time.