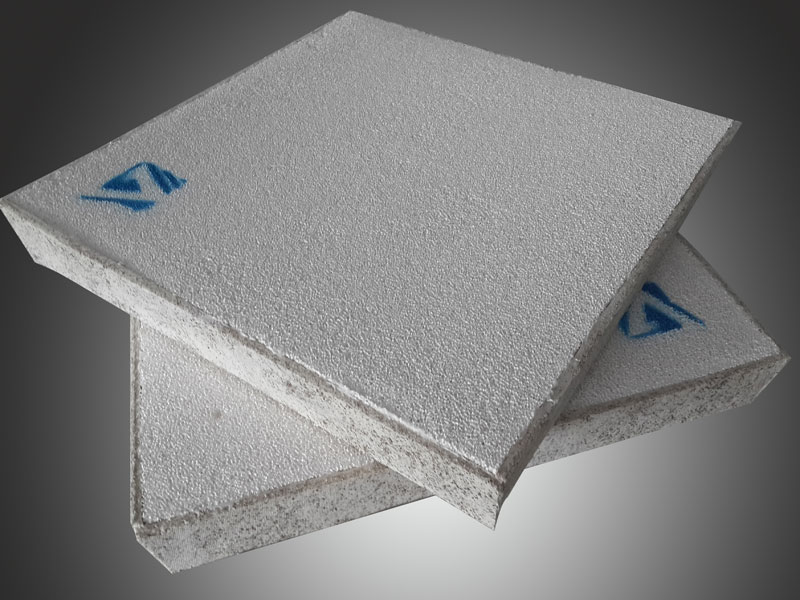
21 2月 Silicon Carbide Foam Filter Aluminum Casting Industry
Silicon Carbide Foam Filter Aluminum Casting Industry
The quality of the aluminum melt is important, which greatly affects the subsequent processing properties and the quality of the final product. Therefore, all countries in the world are very fond of the purification of aluminum melt.
There are many reasons for aluminum pollution. On the one hand, during the melting process, aluminum is exposed to the furnace atmosphere in a molten or semi-molten state, which is prone to oxidation, easily reacts with water vapor to absorb hydrogen, and easily forms various forms of non-metallic slag. (such as furnace lining debris, chlorides, carbides, etc. in the flux) as well as coarse intermetallic particles and the like.
On the other hand, part of the waste material in the composition charge carries some non-aluminum impurities during the circulation. Since the waste comes from the process waste and geometric waste and off-site waste in each process of the factory, the route is different, the composition is complex, and the quality is also poor.
These impurities tend to cause bubbles and inclusions in the slab, which seriously affect the purity of the metal melt, thereby further affecting the processing properties, mechanical properties, corrosion resistance and appearance quality of the product.
The continuous filtration of the aluminum melt by the foam ceramic filter plate is a continuous treatment outside the furnace, and the purification operation mainly includes slag removal.
Silicon Carbide Foam Filter has been used to remove inclusions in aluminum fluids for more than 30 years.
After successful use in production practice, it quickly replaced glass filter, microporous ceramic tube, alumina ball and other filter carriers.
The foam ceramic filter plate has a network hole-like structure and has a certain strength, can withstand the pressure difference of the metal liquid level and the impact of the metal flow, but is brittle and fragile, because the material has a precise structure and a quality, and has Great surface area, so the filtration effect is excellent.
Advantages of using a Silicon Carbide Foam Filter to purify aluminum
After the foam ceramic filter plate purifies the aluminum liquid, it brings great benefits to the strip foil and its products (such as cans, sequins for cars, PS printing plates, etc.), as for the manufacturers of aluminum alloy profiles, Here are a few obvious advantages:
1. Increase extrusion productivity
When using the filter plate to purify the 6063 alloy extrusion blank, we tracked a specific mold and found that the extrusion speed increased by about 20% and the productivity increased by nearly 15%.
2. Extend mold life and reduce the number of mold repairs.
3. Reduce the pressing force
When the filter plate was used to purify the 6063 alloy melt, it was found that the extrusion force was more than 3% lower than the unfiltered.
4. Significantly improved the surface quality of the aluminum profile.
From the above. The use of a foamed ceramic filter plate to purify the aluminum melt has tremendous advantages in terms of reducing production costs and improving product quality.
In addition, the ceramic filter plate is used to purify the aluminum liquid, and the device is an ordinary steel shell lined with a prefabricated refractory brick mat. It is horizontally formulated in the metal flow cell, ie between the flow port and the casting well. There is therefore no need to make major changes to the existing casting system, but only a small space. Moreover, a filter plate can effectively filter all the metal of one melting, and it is very convenient to take out or replace after the end of use. It is also suitable for horizontal or vertical casting systems.
No Comments