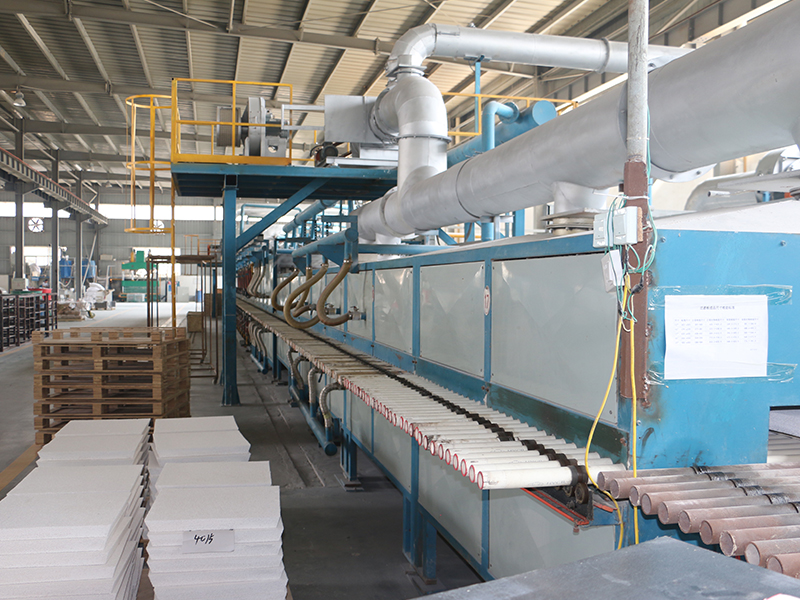
30 3月 Sintered Ceramic Filter
Sintered Ceramic Filter can achieve a larger internal surface area and enhance the effect of deep bed filtration. By reducing the pore size of the filter, the filtration efficiency of molten aluminium can be easily increased, thereby increasing the internal surface area.
The mesh structure of the ceramic foam filter allows a high internal surface area and enhanced deep bed filtration. By reducing the pore size of the filter, thereby increasing the internal surface area, it is easy to improve the filtration efficiency.
Filter cake filtering mainly occurs when the previously captured inclusions prohibit the remaining inclusions from entering the filter structure. Filter cake filtration needs to contain inclusions that can effectively block the inlet of the filter material. Strainers and ceramic foam can be used as cake filters with many inclusions.
Sintered Ceramic Filter provides several key benefits to improve the quality of high-quality aluminum castings. These include
*Improve mechanical properties.
*Reduce signs of dye penetration.
Non-metallic X-ray evidence has decreased.
*Reduce rework/waste.
*Improve processing performance.
The existence of non-metallic inclusions is not conducive to the production of high-quality castings.
The achievable mechanical properties are a key aspect and it is easy to lose the presence of inclusions and scale.
The mechanical properties of high-strength aluminum alloys are very sensitive to nicks or defects in the casting.
Filtration effectively reduces the level of inclusions and the subsequent notch effect caused by inclusions.
Traditional techniques for removing inclusions are ineffective, and the use of metal or fiber barriers is not enough to keep metals away from harmful non-metals.
High-quality castings often limit the acceptability of surface defects found in dye penetrant inspection.
Studies have shown that the level of such defects is reduced when ceramic foam filtration is involved. It has been noted that the indications are significantly reduced or completely eliminated.
Another benefit of using ceramic foam filters is that it reduces non-metallic x-ray evidence.
In these cases, the presence of x-ray defects is often the basis for rejecting expensive castings.
The most important benefit is the reduction of defects visible in areas designated as “structural critical”.
Installing Sintered Ceramic Filter on the running system can protect aluminum castings from harmful non-metallic materials.
Although implemented only by aluminum foundries since the late 1970s, ceramic foam filters are increasingly used to prevent non-metallic materials from entering the cavity, which has led to the demand for high-quality castings in the market today.
The ceramic foam filter was originally developed for the production of forged aluminum alloys. These forged aluminum alloys are used in strict product applications (such as aluminum cans and lid materials, aluminum foil, aircraft extrusions, memory disks, forging materials and metal wires). ) Very high cleanliness is required. The first application in the foundry industry was high-quality aluminum castings for aerospace applications. Since then, it has expanded into commercial casting and automotive applications.
No Comments