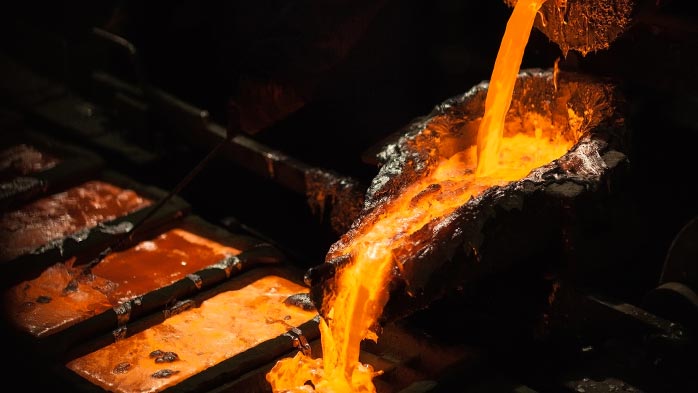
29 11月 Temperature control during melting of aluminum alloy
Temperature control during melting of aluminum alloy
The smelting process must have a sufficiently high temperature to ensure that the metal and alloying elements are fully melted and dissolved.
When the heating temperature is too high, the melting speed is increased, and the time during which the metal and the furnace gas, the lining, and the like are mutually harmful is shortened.
Production practices have shown that rapid heating to accelerate the melting of the charge and shorten the melting time are beneficial for improving productivity and quality.
On the other hand, too high a temperature tends to cause overheating, and particularly when heated by a flame reverberatory furnace, the flame directly contacts the charge, and is strongly heated to the molten or semi-molten metal, which easily causes gas to invade the melt.
At the same time, the higher the temperature, the faster the interaction of the metal with the furnace gas, the lining, etc., and the loss of the metal and the reduction of the melt quality.
Overheating is not only easy to absorb a large amount of gas, but also tends to coarsen the grain structure of the ingot after solidification, increasing the tendency of the ingot crack, and affecting the properties of the alloy.
Therefore, during the smelting operation, the smelting temperature should be controlled to prevent the melt from overheating.
Too low a melting temperature is meaningless in production practice.
Therefore, in actual production, it is necessary to prevent the melt from overheating, accelerate the melting, and shorten the melting time.
Temperature control during melting of aluminum alloy is extremely important.
At present, most factories use high-temperature rapid melting after rapid feeding to expose the metal in a semi-solid and semi-liquid state to a strong furnace gas and flame for a short period of time, reducing oxidation, burning loss and melting of the metal. Inhalation, when a layer of liquid metal appears after the furnace is flattened, in order to reduce the local overheating of the melt, the melting temperature should be appropriately lowered, and stirring is enhanced during the smelting process to facilitate heat transfer of the melt.
In particular, it is necessary to control the melting temperature at which the charge is completely melted.
Due to the latent heat of the metal or alloy, the temperature rises when the charge is completely melted. At this time, if the melting temperature is controlled too high, the metal in the entire molten pool will be overheated.
In production practice, most of the melt superheat that occurs is caused by poor temperature control in this case.
The choice of the actual melting temperature should theoretically be determined based on the melting temperature of the various alloys.
The various alloys have different melting points, i.e., alloys of different compositions, the temperature at which the solid begins to be melted (referred to as the solidus temperature) and the temperature at which the solid is completely melted (referred to as the liquidus temperature) are also different.
In both temperature ranges, the metal is in a semi-liquid semi-solid state.
In order to accurately control Temperature control during melting of aluminum alloy, the melt temperature must be measured. The most accurate method for determining the melt temperature is still by means of the thermocouple meter method.
However, workers with practical experience can judge the temperature of the melt by observing many physical and chemical phenomena during the operation.
For example, the color of the surface of the bath, the degree of dross combustion, and the aluminum or softening of the operating tool in the melt, but these are not absolutely reliable, because it is affected by light and weather and affects its accuracy.
The melting temperature range of most alloys is quite large. When the metal is in a semi-solid, semi-liquid state, such as prolonged exposure to a hot furnace gas or flame, it is most easily inhaled.
Therefore, in actual production, a temperature higher than the liquidus temperature of 50 to 60 ° C is selected as the melting temperature to quickly avoid the temperature range of the semi-molten state.
No Comments