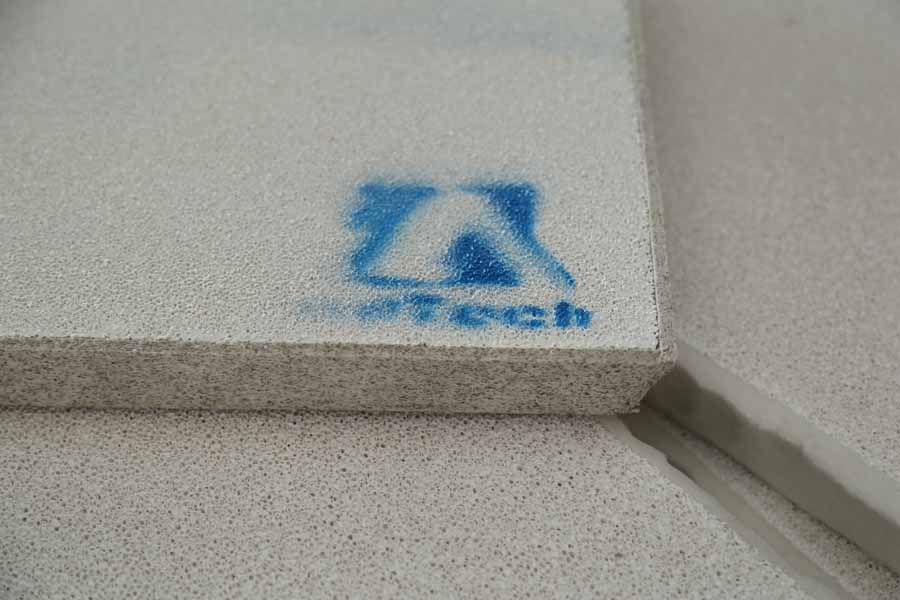
16 6月 The 15th China International Aluminum Processing Summit
“The 15th China International Aluminum Processing Summit”
In 2020, SMM created the “15th China International Aluminum Processing Summit”, and invited leading enterprises in the aluminum processing industry in the country, senior experts, gathered together to present professional views and forward-looking interpretations. “Direction” shares with you the vision of the industry.
In 2020, AdTech will not be absent, and the same will be true of the “China International Aluminum Processing Summit”.
, With an extraordinary beginning, grasp the unexpected future.
As a specially invited star enterprise of “The 15th China International Aluminum Processing Summit”-AdTech, it is advancing with the style of excellence, assisting the summit with technological innovation technology, welcoming friends from the same industry, and studying the development prospects of the aluminum industry. road.
At the meeting, the AdTech CEO’s domestic aluminum melt purification materials and equipment technology trends
To parse. Pointed out the deficiencies of the existing process applications and equipment, and pointed out the main way and development direction of the aluminum alloy melt to improve the purification effect: efforts should be made to realize the localization and popularity of melt purification materials and equipment, so as to improve The overall level.
1. Brief introduction of aluminum melt purification materials and equipment
The gas hydrogen content and solid inclusions in the aluminum alloy melt are the main factors affecting the quality of aluminum alloy products.
The presence of inclusions and gaseous hydrogen destroys the continuity of the metal. Due to the different elastic modulus and expansion coefficient between the inclusions and the metal matrix, the sharp corners of the inclusion phase are prone to stress concentration and become a source of fracture in the material And corrosion source, it is easy to produce various defects during the process of deformation of aluminum alloy materials.
Second, the division and control of the purity of hydrogen and inclusions
2.1 Combined with user requirements and measured data using online hydrogen measurement and slag measurement methods
For ultra-thin aluminum foil, tank materials and other products with first-class purity, the hydrogen content is determined not to be greater than 0.10ml/100gAl, and the slag content is determined not to be greater than 2K/kg;
Aerospace, high-speed rail, double zero foil, can cover materials, CTP plates, automobile plates, rail transit and other important-use products with secondary purity, the hydrogen content is determined to be no more than 0.12ml/100gAl, and the slag content is determined to be no more than 2 -5K/kg;
Common aluminum alloy products such as curtain wall decorative panels with third-grade purity (except for special requirements), the hydrogen content is determined to be not greater than 0.2ml/100gAl, and the slag content is determined to be not greater than 5-80K/kg;
2.2 Production control of aluminum alloy melt purity
First-class purity products: can add first-class waste and use intermediate alloys or aluminum additives-gas refining (Ar2 gas or mixed gas) for remelting flux protection and alloying protection-configuration rotary degassing / vacuum removal Gas-using foam ceramic filter + tube type;
Second-grade purity products: can add second-level waste and use metal additives — gas refining (N2 gas) for flux protection and alloying protection — configuration rotary degassing / vacuum degassing — using two-stage foam ceramics Filter/foam ceramic filter + tubular or deep bed for filtration;
Three-level purity products: can add three-level waste, aluminum scraps and use metal additives — gas refining (N2 gas) for flux protection — using foam ceramic filter;
3. Technical changes in melt purification materials and equipment to improve quality
3.1 Granule refining agent
Replace chlorine gas in furnace and online refining.
Smokeless refining, zero emission of fluoride, fully meet the emission standards set by environmentally friendly harmful air pollution.
The low dosage can control the burning loss caused by the chemical reaction.
Effectively remove alkali metals (Na, Ca, Li)
And non-metallic inclusions, the removal rate is 40%-70%.
3.2 Online degassing equipment
The degassing efficiency is stable at an average of more than 60%, and the inner lining has no pollution, extending the service life.
Solve the industry’s sealing difficulties, high resilience double sealing material, plus built-in air lock seal, to isolate the secondary pollution of air.
The combination of low-conductivity 0.54w/m.k lining material and thermal insulation structure material, the average shell temperature can be controlled at ≤65℃.
The efficiency of removing alkali metals (Na, Ca) is 50-80%.
Sorry, the comment form is closed at this time.