05 12月 Use of electric heating filtration equipment
Use of electric heating filtration equipment
1 Preparation before operation of electric heating filtration equipment
1.1 Install the ceramic fiber cone onto the conical plug connector and secure it. put them into the refractory lining; lower the locking arm into position. Compress ceramic fiber cones and obtain liquid metal by tightening the provided locking bolts
Seal tightly.
1.2 Place the ceramic foam filter into the appropriate position in the refractory lining. Use even downward pressure, making sure to
Securely in place. The filter must be firmly in place to prevent the filter plate from “floating” during the casting process.
1.3 Check whether the parameter settings of the operation interface are correct.
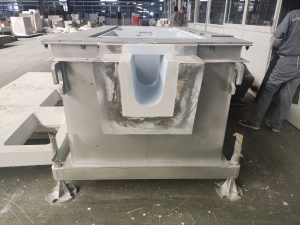
electric heating filtration equipment
2 Equipment baking and preheating (cold preheating and equipment preheating)
2.1 Precautions and curves for the first baking of the filter box
a. Before baking, twist off the vent nuts around the box to allow moisture from the insulation lining to escape.
b. The upper opening of the box should be covered with a 20mm thick fiber blanket the box cover should be well sealed, and the aluminum entrance and exit of the box should be covered with fiber
The blanket is packed tightly and the discharge port is blocked; however, there is a moisture discharge hole of appropriate size before 400℃, and it is plugged after 400℃.
c. Insert the thermocouple into the temperature measuring hole in the box cover and extend it to the middle and lower part of the cavity to control the furnace gas temperature.
d. The normal process temperature of the aluminum liquid in the box is about 750℃, and the furnace gas conduction temperature difference is about 50℃, so the baking
The maximum furnace gas control temperature is 800℃.
e. If the temperature control meter is equipped with a program control function, it will automatically run according to the baking curve setting program, but it is also
Can be controlled manually.
f. If the temperature control meter does not have a program control function, time-stepped manual control will be adopted; power regulator
The maximum current does not exceed the rated current. Records are also recorded at intervals of 1 hour.
g. After the insulation at 800℃ is completed, the filter box can be used for aluminum production. If it is not put into production, the temperature will be reduced to
100℃
Open the cover for inspection, otherwise the lining may be at risk of cracking; or wait until the temperature reaches room temperature before opening the cover again. Don’t open the lid halfway.
3 Equipment use
3.1 Aluminum feeding into the box and constant process temperature
1. Before molten aluminum enters the box, first check whether the connection between the inlet and outlet of the aluminum and the launder is intact, and check whether the bottom
Make sure the drain hole is blocked and blocked.
2. After the empty box is baked to 800°C the heat preservation is completed, and the temperature of the aluminum liquid reaches 750°C, the aluminum liquid can be placed.
3. Remove the refractory fiber wool blocking the aluminum inlet, and then start to pour molten aluminum into the box.
4. During use, when the temperature of the aluminum liquid in the furnace exceeds the set process temperature, the thermostat will automatically stop heating.
heat; when the temperature of the aluminum liquid in the furnace is lower than the set temperature, the thermostat will automatically start heating and slowly reduce the current; making the aluminum liquid
The temperature stabilizes at the set value. Control accuracy ±3℃.
No Comments